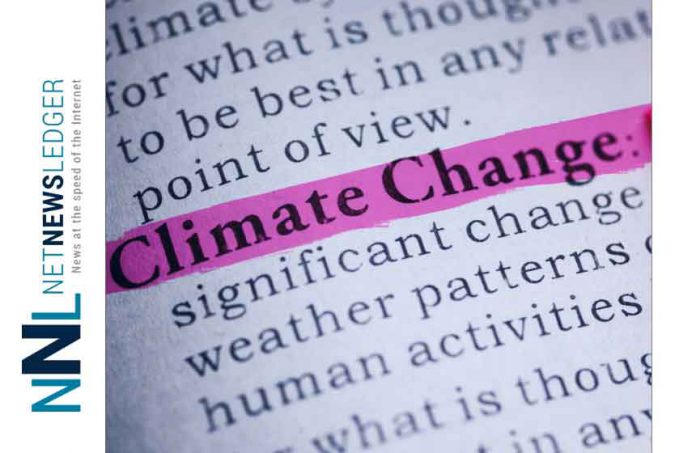
by Eve Pope, Technology Analyst at IDTechEx
When it comes to corporate sustainability and emissions reductions targets, scope 3 emissions (indirect greenhouse gas emissions that occur in a company’s value chain but are not produced by the company itself) are hard to quantify and even harder for businesses to reduce. The embodied carbon from construction can often be a significant contributor, with most of this CO2 coming from the cement used. The IDTechEx report “Decarbonization of Cement 2025-2035: Technologies, Market Forecasts, and Players” explores innovative new green cement solutions that are increasingly enabling companies to decrease scope 3 CO2 emissions. Three of these emerging development areas are explored in this article.
Making cement from new materials
Modern life is built upon billions of tonnes of new concrete each year. Concrete has reliable characteristics, and due to its excellent performance in construction applications it is the second most consumed material on Earth (behind only water). Cement, concrete’s key ingredient, is made from limestone. However, the underlying calcium carbonate chemical composition of limestone means that the CaO compound crucial for cement can only be unlocked by releasing CO2, resulting in a high carbon footprint.
Therefore, green cement players are exploring new starting materials other than limestone that can produce similar or identical cements with well-understood and reliable properties. For example, other cheap abundant calcium sources include basaltic rocks and calcium silicates. Some of the players innovating in this space including Solidia Technologies, Brimstone, Sublime Systems, and C-Crete. Each company has developed its preferred approach to cement-making – from lower-temperature kiln processes, to using electrochemistry, or mechanochemical activation.
Another option, with added circularity benefits, is to reactivate cement paste recovered from demolition concrete. This has been trialed by industry leader Heidelberg Materials via the recycling of captured CO2. Also, start-up Cambridge Electric Cement is developing its own approach based on co-processing during steel-making in electric arc furnaces.
Replace cement with waste materials (new cement chemistries)
The cement sector is no stranger to valorizing waste materials and preventing them from going to landfill. Repurposing waste such as coal fly ash from the energy sector and GBFS (granulated blast furnace slag) from the steel sector as supplementary cementitious materials (partial replacements for cement) is already well-established. But green cement innovators want to take this further, utilizing even greater amounts of industrial waste streams through alternative cement chemistries.
Alternative cements based on alkali-activation and CO2 mineralization for hardening and strengthening are being developed. These different routes can produce cements with desirable properties using increasing amounts of fly ash or steel slag.
Cement alternative space covered in the IDTechEx Decarbonization of Cement 2025-2035 report and relation to conventional OPC (Ordinary Portland cement). Source: IDTechEx
Replace fossil fuels with renewable power
Taking inspiration from the transportation sector, electrifying the cement production process and using renewable energy is another pathway towards cement decarbonization. The difficulty here is achieving the high temperatures required for cement making economically and efficiently that does not involve fossil fuel combustion.
Key development areas include efficient heat transfer and thermal energy storage (to account for the intermittent nature of certain renewable energy sources, such as wind and solar). Finland-based Coolbrook has developed rotodynamic heating technology, which enables fully electric high temperature heat generation up to 1700oC with a high electricity-to-heat generation efficiency. Synhelion’s approach, currently being developed with major cement producer CEMEX, skips the electrification stage by utilizing heat directly from the Sun (concentrated solar power), deploying thermal energy storage and its own solar receiver design. Such technologies are promising not only in the cement sector, but also for decarbonizing other high temperature carbon intensive industries such as steel and petrochemicals.
What does this mean for businesses seeking to lower scope 3 emissions?
While businesses may have limited involvement in the selection of materials when constructing new premises, the green cement space is working to expand access of low-carbon cement to bigger pools of buyers. Over recent years, this may have taken the form of carbon credits, or the emerging book and claim chain of custody model. Already used by some businesses to lower aviation-related scope 3 emissions from transportation/travel via the purchasing of sustainable aviation fuel (SAF), book and claim enables businesses to purchase the sustainability benefits of green cement when access to the physical concrete product is limited. Microsoft championed this environmental attribute certificate approach to cement decarbonization and is expected to become increasingly popular as companies strive to reduce scope 3 CO2 emissions.