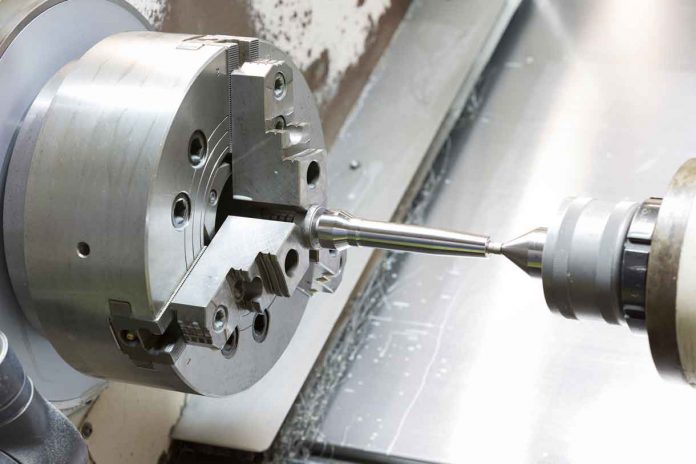
LONDON – Just as the seed that is planted determines the sweetness of the fruit that it will produce in the future, the tool and die design process determines your end result. The design team needs to consider manufacturing design principles to ensure the success of the product. In order to begin the production process, a progressive die is to be designed to the exact specifications in advance. When the tool and die design is carefully planned, inferior objects that are prone to malfunction will not be constructed, resulting in whole product batches being a great success. This helps you avoid the hassle of going ‘back to the drawing board’ and beginning the entire process all over again.
The Tool and die design team could help product manufacturers not only during the production process but also during pre-production. The Tool and die design team assesses blueprints carefully and resolves potential errors in design before commencing work. By ensuring that the product is machine-ready before it hits the presses, a good tool and die design team will save the manufacturer money, time, and unnecessary headaches.
How to understand tool and die?
The tool and die machine is a specialized machine used to shape or cut metal, plastic, and so on, into pre-determined shapes and sizes. Punches, formed into a specific pattern and mounted on a supporting block, are allowed to penetrate into the material, cutting it into the required form.
The tool and die design process
Every tool and die requires a certain amount of designing before it can be built. If the tool and die is more complex such as in progressive dies then more forethought is given to the design. For example, a highly complicated tool may include a lot of detail which would be designed with the help of a CAD system. For faster and more accurate construction, sufficient time is required to finalize the design.
The most essential approach to tool and die design would be to apply a set of design guidelines which outline explicit design goals formulated by the tool and die design team.
The design team must be multi-disciplinary. And the team should include manufacturing managers, product engineers, marketing departments, and cost accountants. Each of those representatives is required to contribute constructively to the design process to make sure that the whole product is designed to exact specifications including functionality, engineering, product branding considerations and budget.
What will affect your end result?
Here are a few steps to bear in mind to ensure that you receive a reliable, high-quality part at the best possible cost.
Tool and Die design Quote
Since each die is unique, price quotes for tool and die design and build can vary. Solid understanding of metal processing techniques and the intricacies of the tool and die design and building process will help companies to provide an accurate quote. Ensure that your supplier is using the latest tool and die design software tools.
Certain factors that influence tooling costs may include the type of tool needed, delivery deadline, volume, contract payment terms and so on.
Progressive die Design
The very first step involves progressive die design. The tool and die design optimizes the position of each punch, hole, and bend in the blank strip. Computer-aided design (CAD) techniques are generally used to design the strip and determine key characteristics such as tolerances, feed direction, dimensions, and scrap minimization.
Tool Production
The progressive die design begins once the stock strip is completed and approved. This would mean that each and every component in the tool is detailed. Now, all the materials for tool are ordered. Dies are machined, ground. At this point working with a single, full-service tool designer can come in very handy, because quality issues and delays are avoided when all necessary processes are kept in-house. Besides, in-house tool and die design is very cost-efficient to produce parts. This way you will not only save money, but you will save time too.
What is the end result of progressive die design?
Progressive die design is one of the best in this sector. For one thing more parts are created in a shorter period of time. Since the larger part of the material is used, the scrap is minimal. Progressive die design allows you a quicker setup time. With a single process, it also allows you to create more Geometries.
Conclusion:
Before choosing a tool and die design team, ensure that they frequently review designs and consult with their customers and have extensive knowledge of the tool and die processes.