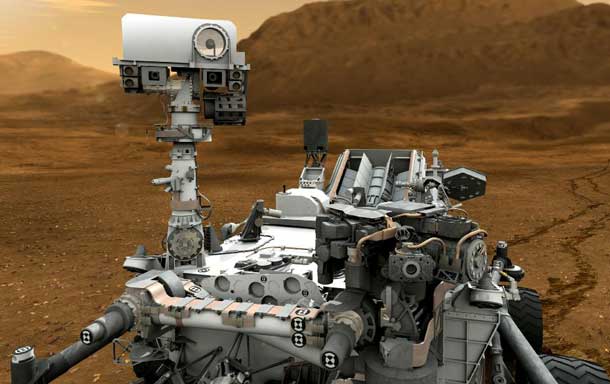
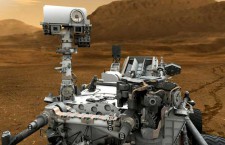
Collaborative robots came into the market in the early 2000’s and since then their use has become widespread in various industries. Research shows that collaborative robots are making industrial a thing of the past as many manufacturers opt to use collaborative robots to automate their operations
Collaborative robots refer to a new breed of robots that is able to work alongside humans in the workplace. They are installed with advanced technology that enables them to avoid collisions promoting safety at the workplace. Some of the common collaborative robots applications in the market include:
1. Pick and place
Pick and place operations in any industry make up for the most repetitive and boring tasks. This can lead to numerous errors if the workers become bored or distracted. The repetitive actions of picking and placing items can lead to strain and injury of the body which might result in numerous legal redress against the company.
Collaborative robots are becoming increasingly useful in the pick and place operations by facilitating the sorting out of particular items from a collection of items. A task which would have taken hours to complete by human beings is now being executed in a matter of minutes by collaborative robotic arm using advanced vision sensors.
2. Machine tending
Manufacturing operations require one or more human workers to stand by a machine and tend to it. The tending process can involve feeding of the raw materials being used into the machine or replacement of the parts of the machine that undergo wear and tear during the production process. Machine tending is not only unproductive to a human being, but also boring and monotonous.
Collaborative robots are very efficient than human beings in doing machine tending at a warehouse. They don’t get bored meaning they are able to look after the machine with maximum concentration at all times. They free up human workers enabling them to carry out more important tasks.
3. Palletizing and packaging
Packaging is an important process in the production of any product. All items require to be packed properly before they can leave the warehouse with some items requiring custom packaging according to customer specifications.
Proper packaging is required to ensure that products are shipped and get to customers in perfect conditions. Collaborative robots are best suited for this process as their level of accuracy is amazingly high. They are also able to handle the wide variety of payloads with ease ensuring safe handling of fragile products.
4. Quality inspection
The advanced vision technology installed on collaborative robots makes them best suited for quality inspection of finished product. They are programmed with the required programmed standards and they benchmark this against the finished products to identify any errors that might have occurred. They can capture images of the finished products and relay that data to a computer where the human operator makes the quality inspection.
5. Processing of tasks
Collaborative robots are involved in the execution of tasks such as gluing or welding which involve the repetition of a certain actions for the completion of the process. Such tasks are not easy to execute especially if the worker is not experienced in doing them and it may take a long time to teach a new employee how to execute them.
Using collaborative robots to execute these tasks is very simple as all it requires is the development of a program that can then be copied onto other collaborative robots. They are also very easy to program such that any worker with basic knowledge of the process being automated can input the commands in the robot to enable it to execute the task.
Conclusion
Collaborative robots are changing the industrial world by enabling manufacturers to automate their daily operations with a very easy and cost effective method. If you are thinking of automating any of the above tasks in your warehouse, you should consider using a collaborative robot.