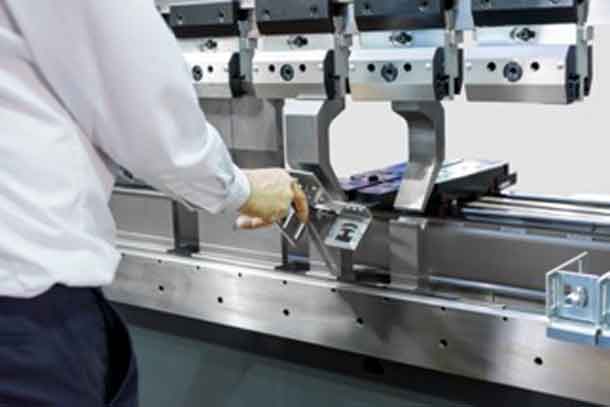
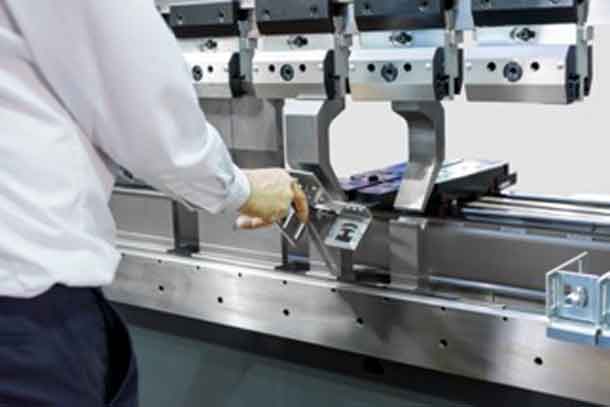
THUNDER BAY – AUTOMOTIVE – A brake press is a big investment. Whether you choose a lower-power mechanical brake press, or a large hydraulic brake press, it can easily cost you upwards of $100,000 – depending on the size and power of the press, of course.
You can save money by getting a used press brake for sale, but even so, you’ll be spending quite a bit of money. Because of this, it’s important to make sure you get the right press brake for your needs.
In this article, we’ll discuss the basics about brake presses, and a few different things you may want to consider when selecting a brake press for your shop. Let’s get started now!
Mechanical Vs. Hydraulic
There are two primary types of brake press in use today – mechanical and hydraulic.
Mechanical brake presses use a motor, which spins a large flywheel at a high speed. Then, a clutch is engaged, mating the flywheel to a crankshaft. This is where the ram of the machine is attached. The crankshaft spins, cycling the ram, and performing the desired operation.
Mechanical brake presses have a few advantages. Electronically, they are very simple, and because of the crankshaft action, the press brake generally can produce tonnages of 2-3x its rated capacity at the bottom of the stroke. This makes them great for punching applications.
The primary disadvantages are that the machine cannot be reversed during operation, and the ram has to complete a full cycle (stroke) – it can’t be interrupted. This can cause some operational limitations and safety hazards.
Hydraulic brake presses use one or more hydraulic cylinders to deliver force to the ram. Hydraulic control allows for finer control and greater precision, and better adjustment for individual bends. They are also usually more quiet, though they lack the sheer force of mechanical models.
Control Type
In the past, brake presses lacked any kind of controls – operation was purely manual. Today, though, most brake presses use a PLC (programmable logic controller) and a CNC controller to streamline the process of bending metal.
This is accomplished with a “backgauge” – a specialized device that automatically moves metal into the proper position for the next bend. Though a CNC-enabled press with a backgauge is more expensive, it’s well worth it for increased production speed.
Bend Style
There are two primary bend styles for bending sheet metal – air-bending and bottoming.
Bottoming, or bottom bending is the simplest method of bending. The ram forces the metal down into the bottom of the die mounted on the press brake bed. This “coins” the material, and overbends it slightly, providing a high-quality, uniform result.
The primary disadvantage of bottoming is that it requires 3-4x the force of “air-bending”, and tooling must be bought for every angle and thickness of bend desired.
Today, fewer than 10% of fabrication facilities use bottoming, because air-bending is superior in almost every way.
Air bending involves pressing the material down onto a die (usually at an 85-degree angle) just far enough to achieve the desired angle. The material is not pressed to the bottom of the die. This is why it’s called “air-bending” – a gap of air exists between the pressed material and the bottom of the die.
This makes it easier to perform a variety of bends with the same die/punch tool combination. However, the accuracy of the angle is harder to control with harder, thicker, materials, requiring constant adjustments.
Tonnage
The best way to choose the tonnage capacity of your machine is with the 80/20 rule. Choose a machine that will be adequate for the 80% of work that you are certain you’ll be doing – not the 20% of projects that you might do in the future.
For example, if you are only bending copper and aluminum for the majority of your projects, it doesn’t really make sense to spend much more money on a press that can handle high-strength stainless steel.
Machine Length
You must choose a machine that’s longer than the maximum length of the parts you wish to bend because the side frames of the machine support both the bed and ram.
In other words, a 12’ capacity press brake may only have 10’ of clearance between the side frames. Make sure to take this into account when selecting your brake press.
Follow This Guide – Find The Brake Press That’s Right For You!
The world of machining can be confusing – so follow this guide to make sure you get the right brake press for your machine shop. You’re sure to get what you need!