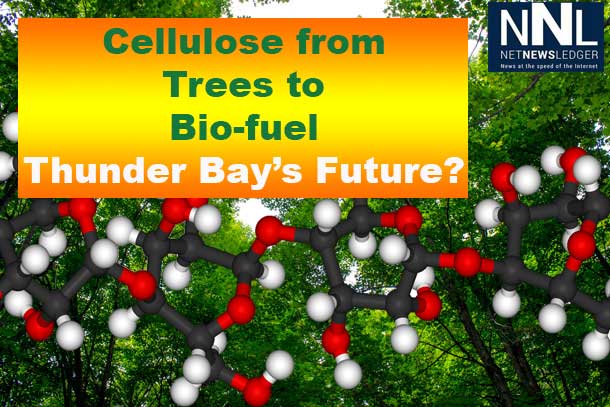
THUNDER BAY – The use of residual forest biomass for rural development faces significant economic hurdles that make it unlikely to be a source of jobs in the near future, according to an analysis by economists at Oregon State University.
In a model of the forest industry, researchers in the College of Forestry combined an evaluation of costs for collecting, transporting and processing biomass with the potential locations of regional processing facilities in western Oregon. Each location was chosen because it is adjacent to an existing or recently-closed wood product operation such as a sawmill or plywood manufacturing plant.
The study, published in Forest Policy and Economics, focused on biomass generated during timber harvesting operations. Biomass consists of branches and treetops that are generally left in the woods or burned. In some highly accessible locations, these residues are ground up or chipped and used to make a product known as “hog fuel.”
“There’s a lot of interest in focusing on the use of biomass to meet multiple objectives, one of which is support for rural communities,” said Mindy Crandall, who led the research as a doctoral student at Oregon State and is an assistant professor at the University of Maine.
“We thought this might provide some support for that idea,” she said. “But from a strictly market feasibility perspective, it isn’t all that likely that these facilities will be located in remote, struggling rural communities without targeted subsidies or support.”
While researchers don’t dismiss the possibility of reducing costs by increasing the efficiency of biomass operations, the future feasibility of such development may depend on public investments and the creation of new markets. And while the study considered the possibility of generating biomass from restoration or thinning operations on federal forestlands, it concluded that the additional supply does little to change the economic feasibility of processing facilities.
It would take changes in technology from transportation to processing as well as the development of new value-added products — such as aviation fuel and industrial chemicals — to improve the economic feasibility of biomass, scientists say.
The study may be the first to combine a model of biomass operations with specific locations for regional processing facilities where the material could be processed and stored. Researchers identified 65 likely locations in western Oregon for such facilities, which they call “depots.”
The cost of harvesting, chipping and loading biomass at timber harvesting sites comes to about $37.50 per dry ton, researchers estimated. Operating costs of a regional depot — including labor, fuel, maintenance, electricity and supplies — would add another $11 per dry ton. These estimates do not include transportation and depot construction.
“The actual levels of these costs that operators experience will be really critical to feasibility,” added Crandall.
Researchers have explored the potential for biomass to be used to make aviation fuel, said John Sessions, an OSU professor of forestry who did not take part in this analysis. Sessions has studied the use of forest harvest residues to produce aviation fuel in a project led by Washington State University. While it is technically possible, the economic feasibility of making aviation fuel from biomass would depend on generating income from co-products as well. The first commercial airline flight using aviation fuel made from forest harvest residues was flown by Alaska Airlines last month from Seattle to Washington, D.C., said Sessions, using residues from this project.
Other efficiencies in biomass processing and transportation could improve economic feasibility, added Sessions. They include reducing its moisture content and increasing its density to reduce trucking costs. The scale of processing facilities could be adjusted to minimize the cost per ton.
Crandall and her colleagues estimated that a depot operating three shifts per day and producing 75,000 dry tons per year would create about 19 jobs.
They also considered the possibility that an increase in material from federal forests would make a difference, but transportation costs would rise because such lands tend to be remote from likely depots.
“Just like with real estate, it’s ‘location, location, location’ that matters here, and national forest lands are not uniformly distributed across the landscape,” said Darius Adams, co-author on the paper. “They are frequently in less accessible areas, and it would cost more to transport material.”
The potential for biomass, the researchers said, will likely depend on the ability to achieve other aims in addition to generating biomass as a product: wildfire risk reduction, forest restoration, energy and rural economic stimulus.
Support for the research came from the Northwest Advanced Renewables Alliance led by Washington State funded through the National Institute of Food and Agriculture in the U.S. Department of Agriculture.