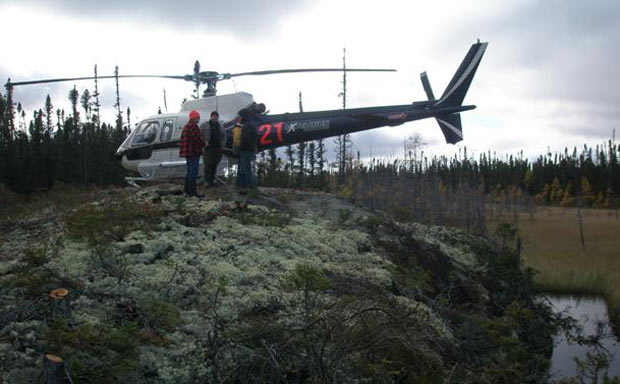
KWG Resources Sets New Direction on Refining
TORONTO – Mining – KWG Resources has filed a patent application for a new method of refining. “It would appear that this process, combining North America’s newly discovered high grade chromite with its also newly discovered wealth of natural gas, could usher a new paradigm into the stainless steel making world,” said KWG President Frank Smeenk. “This process could in any event enable further processing of the Ring of Fire chromite to occur in Ontario, without special exemptions to its domestic electricity price.”
KWG states that this new process will create jobs in Ontario
This means potentially new jobs in Ontario, as using natural gas is far cheaper than even the subsidized rates for electricity.
KWG Resources Inc.’s patent application is in advance of discussions to commercialize a new method of refining into ferro chrome the chromite ore of its Black Horse deposit by means of natural gas. A partial disclosure of the process, summarized from such application, follows:
Background on KWG Patent Application
[sws_pullquote_right]The production of stainless and low alloy steels containing chromium has rapidly expanded, particularly in Asia. The source of the chromium in the stainless steel is partly from the recycling of scrap but this is limited by the availability of such materials, particularly in developing countries. [/sws_pullquote_right] The production of stainless and low alloy steels containing chromium has rapidly expanded, particularly in Asia. The source of the chromium in the stainless steel is partly from the recycling of scrap but this is limited by the availability of such materials, particularly in developing countries. Chromium in stainless steels is not open to substitution by other metals. It is essential for the corrosion and heat resistance of the material. The shortfall in the chromium additions required during the steelmaking process is met by the addition of alloys of chromium and iron, collectively known as “ferro chrome”. These alloys are produced by the smelting of chromite ores, using solid carbonaceous reductants in a Submerged Electric Arc Furnace (SAF). This process is extremely energy and carbon intensive. Existing plants using “best world practices” consume between 3 and 4 megawatt hours (MWH) of electricity and 200 to 300 kilograms of carbon per tonne of ferro chrome alloy produced. Comprehensive gas cleaning systems are required to meet clean air standards. Large quantities of slag are produced and placed in long term storage in above ground dumps.
The development of huge deposits of natural shale gas in the USA and Canada has led to a fall in the long term cost of natural gas and the prospect of stable pricing for many years to come.
There are no commercially viable deposits of chromite ore in the USA and all ferro chrome used in the production of steel is imported, typically from South Africa and Kazakhstan. Recent discoveries of very large deposits of such ores have been made in Canada, a low cost natural gas producer, in a geographic area known as the “Ring of Fire” where this invention could be exploited.
Technology
Large quantities of Directly Reduced Iron (DRI) are currently produced in many countries using existing processes. The current invention uses a modification of this basic and well established technology to produce a chromium iron alloy by using natural gas to reduce both oxides of chromium and iron contained within the ROF chromite ore, the morphology of which has been shown in testing to facilitate the progress of the reduction reactions.
Process Details
Laboratory work has been completed which demonstrates the validity of the process. Samples of chromite ore concentrates from a deposit within the ROF have been successfully reduced to a highly metallized chromium iron alloy suitable for steelmaking. The temperature required for the reduction of chromium is much higher than that for the reduction of iron alone. In order to enable the reduction process to proceed at an acceptable rate at lower temperatures the use of an accelerator has been determined. The chromite ore concentrate is supplied as fines and needs to be agglomerated prior to the reduction stage. This is accomplished by using a disc pelletizer, commonly available for the production of iron ore pellets. It has been shown that carbon is a required additive to the chromite to facilitate reduction.
Usage in steel production
The process outlined above has been shown to produce metallization levels of chromium and iron of 80% or more. Higher metallization rates for both chromium and iron can be expected with process development. The resulting pellets of reduced chromite are suitable for stainless and alloy steelmaking, either as batch or continuously charged components of the steelmaking charge. Substantial cost advantages are expected when compared to the usage of conventionally produced ferro chrome alloys. The carbon content of the reduced chromite is intended to be considerably lower than the ferro alloys produced in an SAF. This will result in significant process advantages for the steelmaker and therefore lower his cost of production. The reduced chromite pellets can form part of the charge of a conventional SAF furnace producing ferro chrome, with significant cost benefits.